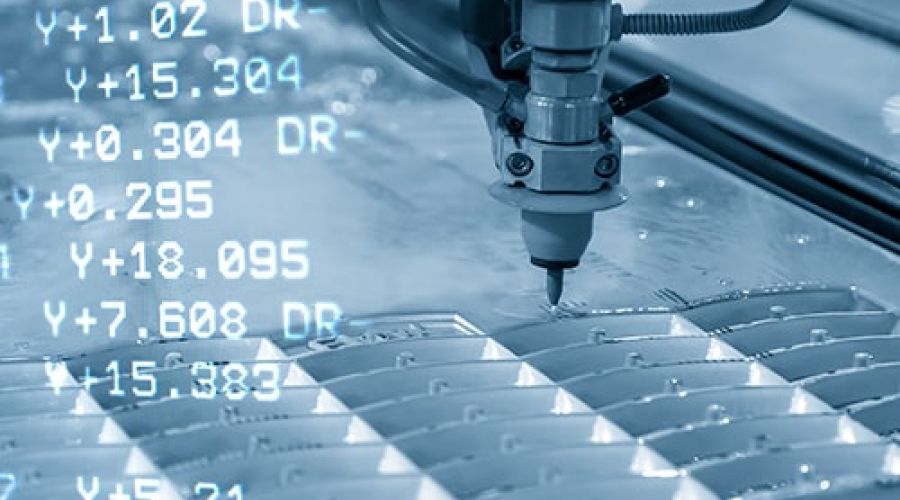
Composite Parts Manufacturing in the Age of Industry 5.0
The composite parts manufacturing sector, known for producing high-performance products, remains heavily reliant on manual labour, despite ongoing advancements in automation. Complex processes like hand lay-up or reinforcement placement are difficult to automate due to their intricacy and variability. While some automated solutions exist, their implementation is particularly challenging for SMEs, requiring substantial investments and extensive reconfiguration of production workflows. This reliance on manual labour also raises significant human-centric challenges, as workers often face repetitive, physically demanding tasks in environments that pose health risks. Furthermore, the sector’s dependence on human expertise leads to inefficiencies and human errors, affecting process consistency. These challenges make the adoption of Industry 5.0 principles—such as human-centricity, sustainability, and resiliency—particularly relevant. Moving forward, the integration of technologies that prioritize worker well-being and enhance system flexibility will be crucial for transforming the sector.
In composite parts manufacturing, human-centricity is vital due to the physically demanding nature of the work. Technologies like digital-twins and AI-driven data analytics are revolutionizing the sector by automating monitoring tasks, such as gelcoating inspection. These solutions eliminate the need for operators to perform visual inspections in harmful environments, promoting safer working conditions. Additionally, cobots have been introduced to reduce the physical strain on workers by handling repetitive or strenuous tasks. For example, cobots assist in moving heavy moulds, relieving operators from such burdens and freeing them to focus on higher-value activities like quality assessments and strategic decision-making. These advancements, combined with automation in hazardous or labour-intensive areas, create a healthier, more fulfilling work environment, where workers are less prone to fatigue and injuries. This shift reflects the human-centric goals of Industry 5.0, aiming for a balance between technological efficiency and human well-being.
Further enhancing human capabilities, AR systems provide real-time instructions and feedback to operators, ensuring accuracy during complex tasks. AR tools enable workers to complete intricate procedures with greater precision, reducing errors while supporting workers’ well-being by minimizing cognitive overload during highly detailed tasks. For instance, AR-guided assembly improves process accuracy, reducing both training time and human errors, which in turn boosts job satisfaction and operational efficiency.
The use of AI-based predictive maintenance tools is another key innovation. Such systems track the condition of critical production equipment ensuring timely interventions before mechanical failures occur. For instance, detecting early signs of wear in components wear prevents costly downtime and production delays, allowing for continuous operations and reducing disruptions. This proactive approach ensures that production remains resilient even in the face of operational challenges, enabling factories to anticipate issues rather than react to them.
Sustainability is a pressing concern in composite parts manufacturing, where raw material waste and energy consumption are traditionally high. The integration of automated quality control systems addresses these issues by detecting production flaws early, preventing defective products from advancing through the production line. This reduction in scrap materials contributes to significant waste reduction, cutting both material and energy waste across the entire production cycle.
Moreover, advanced data-driven process optimization has enabled manufacturers to minimize energy use during critical phases like resin curing. By leveraging real-time data to adjust production parameters, machines operate more efficiently, conserving energy and reducing carbon emissions. The overall environmental footprint is lessened not only by improving energy efficiency but also by avoiding the overuse of raw materials. In addition, sustainable production practices, such as precision manufacturing are gaining traction, further aligning the industry with sustainability goals.
The future of the composite parts manufacturing sector relies on the adoption of state-ofthe-art technologies that align with Industry 5.0, emphasizing human-centricity, sustainability, and resiliency. As advanced manufacturing solutions continue to develop, stakeholders must focus on implementing technologies that reduce the physical burden on workers and improve operational efficiency. For SMEs, overcoming the challenges of high investment costs and complex integration will require collaborative approaches, such as leveraging public funding and forming industry alliances. In addition, manufacturers should prioritize sustainability by adopting practices that minimize waste and energy consumption, ensuring long-term environmental responsibility. To enhance resiliency, stakeholders need to invest in solutions that ensure continuous production and reduce the impact of disruptions. By embracing Industry 5.0 principles, the sector can achieve greater stability and adaptability to evolving market demands and consumer preferences, while enhancing the quality of life for employees and contributing positively to society as a whole.
Leave a Comment
You must be logged in to post a comment.